Our sawmills produce much needed building materials for communities near and far, but did you know they can also produce renewable energy? Byproducts from the lumber making process (AKA residuals) like sawdust, wood chips, and bark can be repurposed as fuel for a variety of uses.
What is Biomass Cogeneration?
Biomass cogeneration is a process that uses organic materials like wood residuals to produce energy. Unlike traditional energy plants that only generate electricity, a cogen simultaneously produces electricity and captures heat that would otherwise be lost.
How it Works at Hampton
The cogeneration process begins with collecting biomass fuel from the sawmill’s operations. Wood waste is funneled into the energy plant’s combustion chamber, where it is burned at high temperatures to create heat. This heat converts water in the boiler into steam, which is then directed into a turbine. As the steam pushes through the turbine, it generates electricity that powers the sawmill and, at times, supplies renewable energy to the local utility. For instance, our Darrington sawmill has a cogeneration facility that supplies the Snohomish County PUD.
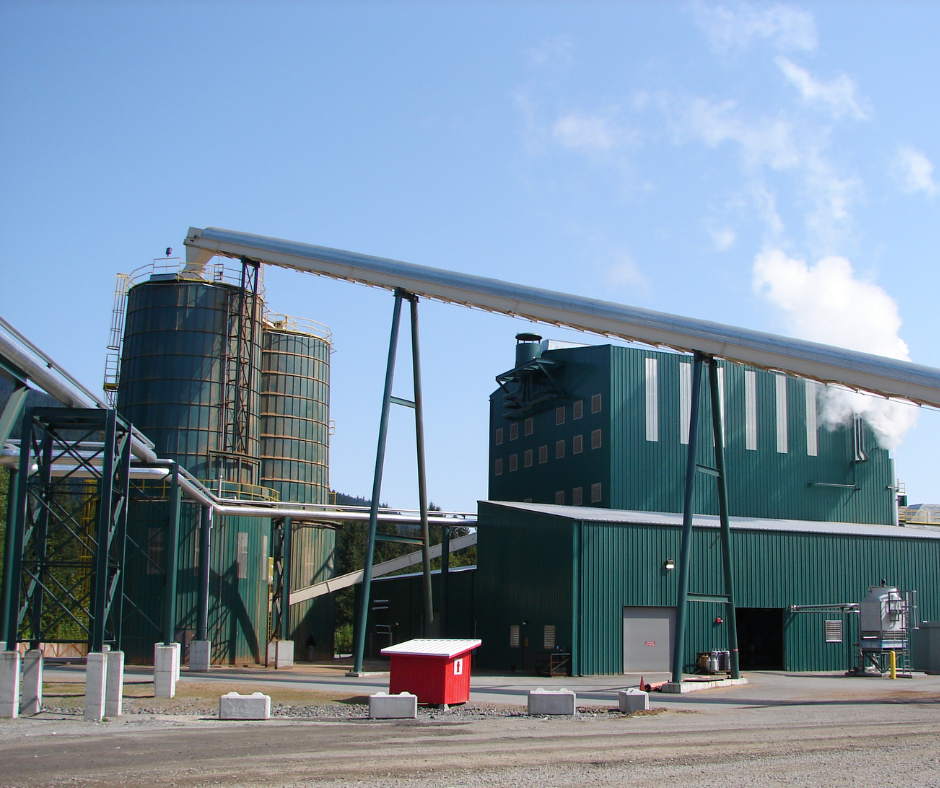
One of the unique aspects of the Darrington cogen plant is its dual-purpose nature. By using the byproducts of lumber production, we not only create a clean energy source but also reduce the need for external power sources. Additionally, the plant captures and uses excess heat generated from combustion for other processes in the mill, including the drying of lumber. This combined production of heat and electricity maximizes the use of each unit of biomass fuel, making the process incredibly efficient.
The Science of Sawdust
The success of our cogen depends on meticulous management of biomass fuel, which is affected by seasonal changes. During the warm summer months, the biomass can become overly dry. This can lead to faster combustion and potentially excessive heat, which is less efficient and may cause operational issues. To counter the drier fuel, supplemental moisture is added to bring the fuel’s moisture content back to an optimal range as it travels along the conveyor belt. In winter, the opposite occurs as moisture levels increase due to rain and snow, so we often mix in dry sawdust to balance the fuel. This careful regulation ensures that the biomass burns at an optimal rate year-round, supporting consistent energy production.
Protecting Air Quality
A crucial component of the Darrington cogen plant’s operation is its Electrostatic Precipitator (ESP), a state-of-the-art system that controls and captures particulate emissions from the burning process before they’re released into our atmosphere. These systems significantly reduce emissions and keep our operations compliant with environmental regulations. Once collected, ash particles can be repurposed or disposed of responsibly.
Why Wood Cogens Rock
- Waste Reduction: Repurposing sawmill byproducts as fuel means less waste needs to be disposed of or transported offsite.
- Renewable Energy Production: Biomass is a renewable resource, unlike fossil fuels. By relying on biomass, we reduce our dependency on non-renewable resources.
- Carbon-Neutral Energy Source: Biomass combustion is generally considered carbon-neutral because the carbon released by combustion was first captured by trees and then re-captured by the trees replanted following harvest. By levering the carbon cycle in this manner, we can use sunlight and water to produce a truly renewable stream of wood products, renewable energy, and heat for manufacturing processes. By using wood waste as fuel instead of hydrocarbons, we can create energy with a lower carbon footprint.
- Community Support: Generating renewable energy locally benefits local communities by reducing emissions and adding to the region’s renewable energy portfolio.